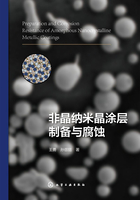
1.1 非晶合金
1.1.1 非晶态合金与金属玻璃
按照物质内部原子的排列结构模型,自然界的物质可以分为有序结构和无序结构两大类。晶体为典型的有序结构,而气体、液体和诸如非晶态固体都属于无序结构。晶体由原子或原子基团呈周期性排列而成,具有长程有序结构;而非晶体中原子的排列缺乏周期性,只是在几个原子的范围(10~15Å,1Å=10-10m)内存在一定的有序度,因而具有长程无序、短程有序的特征,呈现出类似于液态的结构特点,如图1⁃1所示。常见的非晶态固体包括氧化物玻璃(如SiO2)、有机聚合物(大部分工程塑料)和一些半导体单质(如硒、锗等)。

图1⁃1 晶态与非晶态材料的原子排列结构
非晶态合金(amorphous alloys)是指以金属元素作为主要成分,并保持金属特性的非晶态固体,在三维空间成拓扑无序排列,并在一定温度范围保持这种相对稳定状态的合金。它是熔体在连续冷却过程中仍保持液态的“混乱”结构的物质,冷却后得到的原子并非像晶体那样按一定的规律排列,而是长程无序的结构,通常又称非晶合金为金属玻璃(metallic glasses)。与晶态金属材料和普通氧化物玻璃相比,金属玻璃具有很多优异的性能[1,2]。与其他非晶态材料一样,其原子排列相对混乱,缺乏周期性,因而具有均匀、各向同性的结构特征。这消除了晶态金属中因存在晶界、位错、缺陷等带来的对材料性能的不利影响,表现出许多优异的性能,如接近理论值的高强度、高弹性极限(图1⁃2),优异的磁各向同性以及优良的耐腐蚀性能等,因此受到广泛关注。

图1⁃2 非晶合金强度和弹性极限[3]
理论上来讲,只要冷却速率足够快,熔体冷却过程中能够避开结晶的发生,而在玻璃化转变温度冻结,任何金属或合金都可以形成玻璃结构。许多快速凝固技术被用于金属玻璃的制备,尤其是熔体甩带(melt⁃spinning)技术的应用使得许多合金体系能够获得条带或薄片状金属玻璃[3,4]。形成玻璃态结构所需的最低冷却速率称为临界冷却速率(critical cooling rate)。人们一般用合金的临界冷却速率来判断其玻璃形成能力(glass forming ability,GFA)的强弱[5]。而实际上,只有临界冷却速率较低的合金成分才能在实验上形成非晶态结构,纯金属和普通合金成分往往需要极高的临界冷却速率(≫106K/s),才能获得非晶态结构。
1934年Kramer[6]在用热蒸发法制备金属膜研究超导性能时,借助气相沉积法(vapor deposition)制备出非晶态合金Sb,是历史上第一次报道制备出非晶态合金,Kramer也成为最早应用电子衍射来进行非晶态材料研究的科学家。1950年Brenner等[7]发现,当P含量超过10%(原子分数)时,通过电沉积法(electrodeposition)制备非晶态Ni⁃P合金膜,形成超硬表面涂层。1958年Turnbull等人[8]讨论了液体深过冷对玻璃形成能力的影响,揭开了通过连续冷却制备非晶合金的序幕。1960年,加州理工学院一位很有创造性的冶金学家Pol Duwez[9]采用熔体急冷法,成功制备了Au⁃Si非晶态结构合金,这是非晶合金制备历史上一个重要的里程碑。Pol Duwez也被公认为是液相急冷技术制备非晶态合金的创始人,是第一位从研究者的角度明确研究液相快速冷却在冶金上的重要性。
若玻璃形成临界尺寸超过1mm,则称为块体金属玻璃(bulk metallic glasses,BMG)。1984年,Turnbull等人[10]在哈佛大学成功制备了直径8mm的Pd40Ni40P20块状非晶合金,标志着块体金属玻璃问世。众多研究者潜心于非晶合金的研究,如日本广岛大学Yoshinori Isomoto Oka,日本东北大学Akihisa Inoue、Koji Hashimoto,美国弗吉尼亚大学John R.Scully,美国劳伦斯·利弗莫尔国家实验室(LLNL)Joseph Farmer,韩国延世大学Do Hyang Kim,韩国科学技术院Eric Fleury,美国橡树岭国家实验室Chain T.Liu,挪威皇家科学院Marit Bjordal,中国香港理工大学CHENG Fai Tsun、H.C.Man等。
此后,众多块状金属琉璃被开发问世。目前,已经开发的非晶合金体系种类众多,从早期的贵金属系Au⁃(Au49Ag5.5Pd2.3Cu26.9Si16.3,临界尺寸5mm)等,逐渐到Zr⁃(Zr41.2Ti13.8Cu12.5Ni10Be22.5,临界尺寸50mm),Pd⁃(Pd40Cu30Ni10P20,临界尺寸72mm),Cu⁃(Cu46Zr42Al7Y5,临界尺寸10mm)和稀土基(La65Al14Cu9.2Ag1.8Ni5Co5,临界尺寸30mm)等系列,以及近年来成本经济的Fe⁃(Fe41Co7Cr15Mo14C15B6Y2,临界尺寸16mm),Ca⁃(Ca65Mg15Zn20,临界尺寸15mm),Ti⁃(Ti40Zr25Cu12Ni3Be20,临界尺寸14mm),Co⁃(Co48Cr15Mo14C15B6Er2,临界尺寸10mm),Ni⁃(Ni60Pd20P17B3,临界尺寸12mm),Mg⁃(Mg54Cu26.5Ag8.5Gd11,临界尺寸25mm),Pb⁃(Pt42.5Cu27Ni9.5P21,临界尺寸20mm)等临界尺寸可达毫米乃至厘米级的大块合金体系相继研发。
每种体系合金拥有其独特的性能。其中,与其他的非晶合金如Pd⁃、Zr⁃等资深的合金体系相比,铁基非晶合金的制备原料丰富、成本低廉、合成工艺相对经济简单,更主要的是它保持了原有基材的结构组织和综合优异性能的同时,还可以延伸非晶合金所体现出来的功能性并加以利用。
1.1.2 铁基非晶态合金
非晶合金具有非常优异的适合作大型变压器的磁性性能,并具有适合作磁头、电子装置用变压器和各种传感器的磁性和力学性能的综合性能,在各种磁性器件中的应用前景是非常乐观的。自1967年第一个铁基非晶态合金Fe⁃P⁃C[11]出现以后,优异的软磁性能一直是人们关注的热点。此后,Fe⁃Co⁃P⁃B和Fe⁃Co⁃Si⁃B[12]非晶薄带被广泛用作软磁材料。纳米晶Fe⁃Si⁃B⁃Cu⁃Nb[13]和Fe⁃(Zr,Nb)⁃B[14]非晶薄带的开发,进一步推进了非晶态合金作为软磁材料的应用。直到1995年,在Fe⁃Al⁃Ga⁃P⁃C⁃B合金系中成功制备出第一个铁基块体非晶态合金后[15],具有良好软磁性能的铁基块体非晶态合金吸引了众多学者的研究兴趣。2002年,较为廉价的高耐蚀且具有高玻璃形成能力的Fe75-x-yCrxMoyC15和Fe43Cr16Mo16(C,B,P
合金体系被开发,该体系在室温或室温以上未呈现磁性,所以被称作无磁非晶态合金。尽管铁基非晶在尺寸上没有明显的突破,但其高耐蚀性和室温无磁性使得其应用领域更加广泛。2004年,美国橡树岭国家实验室的Liu和弗吉尼亚大学的Poon等人在Fe⁃Cr⁃Mo⁃C⁃B系块体非晶的基础上,利用稀土元素Y和Ln(镧系元素)进行微量掺杂后显著提高了其玻璃形成能力。其中,非晶态合金(Fe44.3Cr10Mo13.8Mn11.2C15.8B5.9)98.5
和Fe48Cr15Mo14Er2C15
均呈现出很强的玻璃形成能力,用铜模吸铸法得到的铁基非晶态合金的最大尺寸达12mm,并被命名为“非晶钢”。非晶钢在室温下呈无磁特性并具有高硬度(显微硬度高达13GPa)、高耐蚀性等特点,这一突破性的进展,使其作为无磁性材料和结构材料更具应用价值。2005年开始,沈军[20]从物理冶金的基本理论出发,采用合金化方法,大幅度地提高了铁基合金的玻璃形成能力。通过以Co部分取代Fe,获得了直径达16mm的无磁性非晶钢(FeCoCrMoCBY),为国际上玻璃形成能力最强的铁基大块非晶合金,从热力学和动力学等方面揭示了这种合金具有高玻璃形成能力的内在原因。此后,设计出具有高非晶形成能力和超低磁性的铁基非晶合金成分,研究了Cu对Fe48-xCuxCr15Mo14C15B6Y2(x=2,5,9,14)合金非晶形成能力、热性能、磁性能的影响规律。并基于二元深共晶合金熔体按一定比例混合后原子之间的相互作用可以达到平衡,从而使晶体相的析出受到抑制这一基本思想,提出了一种快捷、有效的设计大块非晶合金成分的新方法——二元共晶成分比例混合法,为低成本非晶合金材料的工业化应用奠定了重要基础。
自此,铁基非晶合金成为人们研究的热点,由于其具有高强度、强耐蚀性、优异的玻璃形成能力、低廉的价格及相对简单的制备工艺等,有望使其作为新型的工程材料得以应用[21,22]。
非晶态合金被誉为继钢铁和塑料后材料领域的第三次革命,随着该类材料工程化应用推进,对腐蚀问题的关注显得尤为重要。非晶态合金具有单相均匀的结构特征及成分设计的灵活可控性,这些为深入研究腐蚀问题提供了全新的视角。
1.1.3 腐蚀与电化学
腐蚀英文的corrosion起源于拉丁文“corrdodere”,意思为损坏或腐烂。腐蚀的定义众多,曹楚南在《腐蚀电化学原理》一书中对腐蚀的定义是“金属材料由于受到介质的作用而发生状态的变化,转变成新相,从而受到破坏”。托马晓夫定义腐蚀为“由于外部介质的化学作用或电化学作用而引起的金属的破坏”。J.C.Scully则认为腐蚀可定义为“金属材料与其周围介质之间的反应”。U.T.Evans认为“腐蚀是金属从元素态转变为化合态的化学变化及电化学变化”。M.G.Fantana通过归纳得出,腐蚀可以从以下几个方面定义:①由于材料与环境及应力作用而引起的材料破坏或变质;②除了机械破坏以外的材料的一切破坏;③冶金的逆过程。而国际腐蚀工程师协会(NACE)对腐蚀的定义为:材料(通常是金属)由于和周围环境的作用而造成的破坏。
可见,腐蚀是指材料与环境间的物理和化学相互作用,使材料性能发生变化,导致材料、环境及其构成系统受到损伤。狭义上讲,腐蚀指金属材料在特定环境条件下的失效形态,例如铁在大气中的生锈等。但从广义上来说,塑料、陶瓷、混凝土和木材等非金属材料由化学作用使其消耗或破坏也属于材料腐蚀的范畴,例如,涂料和橡胶由于阳光或者化学物质的作用引起变质、老化等。
依据反应历程,腐蚀可分为化学腐蚀和电化学腐蚀两类。当材料处于无水条件下,环境中的气体分子或原子会优先在材料表面吸附,并通过化学反应造成材料的腐蚀,称为化学腐蚀。通常,在环境中有水参与的条件下,腐蚀服从电化学动力学基本规律,属于电化学腐蚀范畴。由于地球大气中普遍含有水,化工生产中也经常处理各种水溶液,因此,电化学腐蚀是地球上最常见的腐蚀类型。
(1)腐蚀的重要性
自从人类社会进入钢铁世界,腐蚀的危害便如影随形——它就像一种慢性毒药,发展过程极为缓慢,易被人们忽视,但往往会酿成重大安全事故。腐蚀具有自发性、普遍性和隐蔽性等特点,对人类生活和工业发展来说,腐蚀的危害是惊人的。因为腐蚀,美国旧金山San Mateo⁃Hayward跨海大桥使用不到20年,就耗巨资进行了修补。著名畅销书作家与环境调查记者乔纳森·瓦尔德曼(Jonathan Waldman)在他首部著作《腐蚀》(RUST:The Longest War)中指出,腐蚀是毁灭美国的恶魔,它掘开了人类的墓穴。
据估计,工业世界生产的钢材因腐蚀而报废的占年产量的1/3左右。据统计,全世界每年因金属腐蚀造成的直接经济损失约7000亿~10000亿美元,工业发达的国家尤为严重,由金属腐蚀引起的直接经济损失约占国内生产总值(GDP)的2%~4%。比如,英国近年来因腐蚀造成的年损失达100亿英镑,占GDP的3.5%;德国的年损失约为450亿德国马克,占GDP的3.0%;美国年腐蚀损失达3000多亿美元,占GDP的4.2%。2016年10月,NACE“全球腐蚀调研项目研究报告”显示,腐蚀失效占GDP的3.4%。2016年6月,中国工程院重大咨询项目“我国腐蚀状况及控制战略研究”表明,2014年我国腐蚀总成本超过2.1万亿元人民币,约占当年GDP的3.34%,腐蚀给人类造成的危害和损失甚至超过风灾、火灾、水灾和地震等所有自然灾害的总和。
正确适当的防腐措施则可以降低腐蚀损失15%~35%,这也是人们需要研究腐蚀规律和机理的关键所在。我国的杭州湾海域的泥砂含量高、水流速快,存在较多微生物,目前杭州湾大桥、港珠澳大桥联合使用中国科学院金属研究所自主研发的高性能防腐涂料与阴极保护,并结合腐蚀原位监测技术,保障了杭州湾大桥100年和港珠澳大桥120年的设计寿命。防腐蚀不仅仅是科学与技术问题,同时也是管理问题。防腐蚀最好的方法就是做好事前防控。科研人员要深入认识腐蚀发生的机理,技术人员要诊断出腐蚀发生的“病因”,企业要在生产过程中规范防腐蚀设计、合理选择耐蚀材料和防腐蚀方法,在工程装备使用过程中要重视日常维护,最后要重视长寿命工程结构的安全评价与寿命预测,这样才能最大限度地降低腐蚀危害。
今天,腐蚀机理的基础研究、防腐蚀技术研发、防腐蚀工程控制等,已经成为人类的重要课题。腐蚀对经济、环境、安全的巨大影响使得各国投入巨大的人力和经费从事腐蚀防护领域的基础研究。同时又由于腐蚀科学涉及物理化学、金属学、电极过程动力学、材料学、固体物理与表面科学等基础学科,对腐蚀科学的研究会涉及多种学科中的科学前沿问题。
从太空到地面乃至水下与地下,从金属材料到非金属材料,腐蚀无处不在。正如腐蚀科学家柯伟所述,“金属腐蚀是悄悄进行着的材料失效和破坏,相当于无焰的火灾,也是材料和设施的癌症。在解决有限资源的利用、环境保护和未来生态城镇建设过程中腐蚀与防护作为一项可供直接利用的重要技术应该充分发挥作用。我们期望全社会能够像关注环保和疾病治疗一样,关注腐蚀问题。”我国已经进入基础建设高峰期,如果不重视防腐蚀,未来与腐蚀相关的重大安全事故很有可能频繁发生,重视腐蚀,从今天开始。腐蚀是安全问题、经济问题、生态文明问题、国计民生问题、节约资源问题。因此腐蚀防控力度是国家文明和繁荣程度的反映。
(2)腐蚀学科发展历程
腐蚀是一门有非常悠久历史的古老学科。人类对腐蚀现象的观察及其防护措施的探索可以追溯到数千年前的古代。
3000年前,我国商代用锡改善铜的耐蚀性,发明锡青铜;2000年前,秦始皇兵马俑坑中青铜剑光亮如新,锋利如初,表面有10μm厚含铬黑色氧化物,类似现代铬酸盐钝化处理;2000年前,古希腊Herodus和古罗马Plinins已提出用锡防止铁生锈。
1748年,Jlomohocob解释了金属的氧化现象;1763年,Alarm认识到了双金属接触腐蚀现象;1790年,Keir描述了铁在硝酸中的钝化现象;1801年,W.H.Wollaton提出了电化学腐蚀理论;1824年,Davy用铁作为牺牲阳极,成功实施了英国海军铜船底的阴极保护;1827年,A.C.Becquerel和R.Mallet先后提出了浓差腐蚀电池原理;1830年,De·La·Live提出了金属电化学腐蚀的经典理论,即微电池理论;1840年,Elkington正式获得电镀银专利;1847年,Aide发现了氧浓差腐蚀现象;1887年,S.Arrbeius提出了金属离子化理论;1890年,Edison研究了通过外加电流对船实施阴极保护的可行性。
20世纪上半叶是腐蚀科学发展的黄金时代,基于石油、化工等行业的蓬勃发展,促进了腐蚀理论和耐蚀材料的研发,确定了金属腐蚀和氧化的基本规律,奠定了腐蚀理论基础。腐蚀科研机构纷纷成立,腐蚀科学系统化,理论水平极大提高。
1906年,美国材料与实验协会(ASTM)建立大气腐蚀试验网;1910年,防腐蚀涂料问世;1911年,Eden首次观察到微动腐蚀现象;1912年,美国国家标准局启动了历时45年的土壤腐蚀试验;1923年,Tammann、Pilling与Bedworth提出氧化动力学定律和氧化膜完整性的判据;1926年,AcAdam着手研究腐蚀疲劳;Whitney提出腐蚀金属表面形成的电池电动势控制着腐蚀速率,英国冶金科学家Evans通过实验证明了这种电池,并于1929年绘制了腐蚀极化图,提出金属腐蚀的电化学基本规律,推动了电化学腐蚀的动力学研究,腐蚀科学真正意义上得以建立;1933年,Wagner从理论上推导出金属极化图,推导出高温氧化膜生长经典抛物线理论;1938年,Wagner和Traud建立了电化学腐蚀的混合电位理论,奠定了近代腐蚀科学与工程动力学基础;1938年,Pourbaix提出Fe⁃H2O体系电位⁃pH图,确立腐蚀与电位和pH的定性关系,为理论上判断腐蚀倾向及探索控制腐蚀途径提供了依据,奠定了腐蚀热力学基础;1938年,Brenner和Riddell提出化学镀镍技术。
到20世纪下半叶,腐蚀学科发展为独立的综合性边缘学科。现代工业迅速发展,原先大量使用的高强度钢和合金出现严重的腐蚀,促使相关学科(现代电化学、固体物理、断裂力学、材料科学)的学者们对腐蚀问题进行综合研究。如:1950年,Uhlig提出了点蚀的自催化机理模型;1957年,Stern发表了一个著名线性极化求解腐蚀速率的Stern公式。从理论上导出了在靠近腐蚀电位的微小电位区间(±10mV),腐蚀电流与极化电阻成反比,根据这一规律创新了快速测定腐蚀速率的线性极化技术。1960年,Brown首先将断裂力学应用到应力腐蚀研究中;1968年,Iverson观察到了腐蚀的电化学噪声信号图像;1970年,Epellboin首次用电化学阻抗谱研究腐蚀过程。
随后,扫描电子显微镜、俄歇能谱仪等先进材料分析仪器在腐蚀研究中的应用,进一步提示了更多腐蚀问题的微观本质。同时,腐蚀学科形成了许多边缘腐蚀学科分支,如腐蚀电化学、腐蚀金属学、腐蚀工程力学、生物腐蚀学及腐蚀防护系统工程等,腐蚀领域及其相关的研究方兴未艾。
(3)腐蚀电化学学科发展历程
腐蚀过程和腐蚀的防护主要涉及电化学作用,腐蚀与电化学学科紧密相连。从基础学科发展看,电化学主要研究电子⁃离子导体、离子体⁃离子导体界面现象、结构化学过程及与此相关的现象,被认为是隶属物理化学(二级学科)的一门三级学科,发展重点从属物理化学发展重点。
电化学发展早期,从属原子分子学说(如法拉第定律和电化学当量)。1791年,意大利解剖学家Galvani解剖青蛙时发现解剖刀或金属能使蛙腿肌肉抽缩的“动物电”现象,这是人类历史上第一个发现的电化学现象,标志电化学学科诞生。Galvani认为蛙腿痉挛是由生物本身产生的动物电流引起的。1794年,意大利物理学家Volta开始阐释Galvani实验的本质,认为产生电流不需要动物组织。Volta越过Galvani的原始实验,开始研究两种金属接触产生的电流(“金属的”电流),之后又研究金属浸入某些液体时的电效应,最终于1799年发明了伏打电堆/池。这是世界上第一个能产生稳定、持续电流的化学电源。有了持续电流,才对电学的研究打开了新的局面。1800年,Nichoson和Carlisle利用伏打电堆电解水溶液,发现两个电极上均有气体产生。这是电解水第一次尝试,是最早的电化学事例,电化学由此进入起步阶段。1834年,Davy的助手Faraday定量研究有关电化学现象,发现当电流通过电解质溶液时,两极上会同时出现化学变化。Faraday通过对这一现象的定量研究,发现了电解定律。电解定律的发现,把电和化学统一起来了,这使Faraday成了世界知名的化学家,电化学理论获得进一步发展。1855年,Fick提出扩散第一定律和第二定律,解析了扩散过程的特征。1873年,Gibbs提出热力学定律,从理论上全面地解决了热力学体系的平衡问题。1879年,Helmholtz等提出双电层紧密型模型。1889年,Arrhenius提出经验公式,改变活化能可以改变化学反应速率,改变电极电位通常可以改变电化学反应的活化能,从而也可以影响电极反应的速率,将活化能和反应速率建立联系。
此后,进行电极过程热力学的研究阶段。1889年,Nernst提出溶解压假说,从热力学方面导出电极势与溶液浓度的关系式,即电化学中著名的Nernst方程。Nernst方程将电位和溶液浓度的关系统一起来,从此热力学数据便可用电化学的方法来测量,电化学热力学理论趋于完善。Nernst在解释电极电位产生的原因的同时,提出了双电层理论。1905年,Gouy和Chapman提出双电层分散型模型。1905年,Tafel在实验中发现,许多金属表面上析氢超电压服从实验公式η=a+blgi,解释了电流密度和电极电位的关系。1920年,Debye⁃Hückel提出强电解质离子互吸理论(也叫非缔合式电解质理论)。1924年,Stern提出双电层紧密⁃分散型模型,自此紧密型、分散型、紧密⁃分散型三个双电层模型已完全建立,Stern紧密⁃分散型模型清晰地解析了电极/溶液界面双电层结构特征。1929年,Evans将代表腐蚀电池特征的阴、阳极极化曲线画在一张图上,只考虑腐蚀过程阴、阳极极化性能相对大小,不考虑电极电位随电流密度的变化,从而将理论极化曲线表示为直线,并用电流强度代替电流密度作横坐标,得简化腐蚀极化图,方便进行腐蚀阳极和阴极极化性能研究。Evans成为20世纪最伟大的腐蚀电化学和动力学家。1930年,Butler和Volmer提出电极过程动力学方程,描述电子转移步骤的稳态电流密度与过电位的关系,反映了电极净反应速率随电极电位改变而变化的规律,称为Butler⁃Volmer公式,至此电极过程动力学体系基本形成。1938年,Pourbaix提出Fe⁃H2O体系电位⁃pH图,确立腐蚀与电位和pH的定性关系,电位⁃pH图是判定腐蚀发生,研究腐蚀反应、行为、产物,以及提出腐蚀控制途径的理论框架。Pourbaix和同事作出90种元素与H2O构成的电位⁃pH图,并向多元以及高温方向发展,为腐蚀科学作出了卓越贡献。Evans高度评价:“如果当代杰出的数学家为他们创立的微分方程而欣喜……,则今天的腐蚀学家应为Pourbaix图的建立而拍案叫绝。”
很长时间,电化学家企图用化学热力学解决一切电化学问题,认为极化由传质过程引起(Nernst公式),忽略电化学电荷转递也影响。20世纪40年代后,“电极过程动力学”异军突起,曾领风骚四五十年。电化学瞬态研究方法的建立和发展,促进了电化学界面和电极过程宏观动力学研究的迅速发展。
20世纪50~70年代,电化学主要受动力学派控制,但所描述的动力学理论与公式多数是唯象的理论(B⁃V公式),更多是经验公式(Tafel公式),缺乏微观的机制与机理的解释。1956年,Marcus提出电子/电荷转移Marcus理论。电子和外层电子的转移提供热力和动力学框架,可以在电荷转移方面,弥补Tafel经验公式和唯象B⁃V公式的缺点,获1992年诺贝尔奖。1957年,Stern发表了一个著名线性极化求解腐蚀速率的Stern公式。1985年,曹楚南著《腐蚀电化学原理》,论述了腐蚀电化学的特殊规律,形成了比较完整的理论体系,并将数理统计和随机过程理论应用于腐蚀科学中,提出了利用载波钝化改进不锈钢钝化膜稳定性的思想。同时,还将定态过程稳定性理论引入电化学阻抗谱(EIS)研究,使EIS理论有了重要发展。
从20世纪70年代起,随着检测分子水平信息的原位谱学电化学技术的建立,电化学进入由宏观到分子水平,由经验及唯象到非唯象理论的研究阶段。随着固体物理理论和第一性原理计算方法的广泛应用,以及各种特殊功能的新材料的出现,一门以综合材料学基本理论实验方法与计算方法为基础的电化学新学科正在形成。
另外,电化学交叉新兴学科也正在兴起,如光电化学、能源电化学、材料电化学、纳米电化学、环境电化学、腐蚀电化学等,电化学领域及其相关的研究发展得如火如荼。
1.1.4 铁基非晶态合金耐蚀性能
非晶态合金的结构和成分的高度均匀性以及能够在表面迅速形成均匀、致密和覆盖性能良好的耐蚀钝化膜等特性,使得铁基非晶态合金呈现出良好的耐腐蚀性能。在研究钝化膜快速生长方面的实验中发现,无膜状态下的铁基块体非晶态合金的表面化学活性比较大。因此,一旦铁基块体非晶态合金的钝化膜遭到破坏,在其表面能够迅速生成厚的钝化膜,增进块体非晶态合金的耐蚀性。另外,非晶态合金中的微量元素添加对钝化膜的形成能力和稳定性也有很大的影响[23]。
日本学者Naka[24]等早在1974年就系统报道了Fe⁃Cr⁃P⁃C金属玻璃具有优异的耐腐蚀性能。与传统晶态304不锈钢相比,Fe⁃Cr⁃P⁃C金属玻璃即使在高浓度HCl溶液中仍无明显失重,由此也激发了对高耐蚀非晶合金的研究与开发。此后的近20年里,Hashimoto研究组相继研发出数十种具有优异耐蚀性能的非晶态合金[25]。除了Fe(Ni)⁃Cr⁃P⁃C体系外,还包括Ni⁃Nb、Ni⁃Ta等非晶合金。
非晶态合金的耐蚀性主要表现在其突出的耐点蚀性和优异的钝化行为。铁基非晶态合金Fe⁃Cr⁃Mo⁃P⁃C⁃B具有优异的耐腐蚀性能,即使在12mol/L的盐酸溶液中阳极极化至1V(Ag/AgCl)时也不会发生点蚀[26];块状Fe⁃Cr⁃Mo⁃P⁃C⁃B合金[27]在1mol/L HCl溶液中表现出很强的耐腐蚀性能,极化曲线上存在很宽的钝化区,钝化电流密度约10-2A/m2,同时在6mol/L和12mol/L HCl溶液中,当阳极电压达到1.5V(Ag/AgCl)时均未发生点蚀。Fe48Cr15Mo14Y2C15B6和Fe50Cr18Mo8Al2Y2C14B6块体非晶态合金在模拟燃料电池环境下的耐蚀性能远远超过316不锈钢[28];Fe60Co8Zr10Mo5W2B15块体非晶态合金在298K的王水中浸泡3600s后基本无失重[29]。铁基非晶态合金的腐蚀速率(0.01mm/a)远远低于304不锈钢及纯铬等(100mm/a)[30]。30℃时在海水介质中,铁基非晶合金比316L不锈钢和C⁃22镍基合金具有更高的点蚀电位,钝化性能更稳定[31]。
人们对非晶态合金的耐蚀性研究给予了非常多的关注,相继发现了一系列具有良好的玻璃形成能力的高耐蚀非晶态合金,并对其耐蚀机理进行了深入研究[17,30⁃37]。非晶合金的耐腐蚀性能与成分有很大的关系。Naka等[24]研究表明,除了Mn外,向Fe⁃P⁃C非晶合金中添加不同的合金化元素,如Ti、Zr、Cu、Mo、W、V、Nb、Ni和Co等,均可以不同程度地提高其耐腐蚀性能。Hashimoto等[25]采用X射线电子能谱(XPS)分析腐蚀表面成分,详细表征了数十种非晶态合金表面钝化膜的成分组成,解释了诸多合金元素的作用。将腐蚀过程中能够形成稳定钝化膜的元素称作耐蚀性元素,如Cr、Nb、Ta、Ti、Mo等,认为这些合金元素决定着钝化膜的稳定性,进而对腐蚀性能优劣起关键作用。Hashimoto和Asami等[38]还认为两种或两种以上耐蚀性元素共同形成的钝化膜会更加稳定。其依据是耐蚀性阳离子之间的协同效应,形成复杂的氧化物保护膜。对于最早报道的耐蚀性较好的Fe基非晶合金体系,Cr与Mo的联合添加也能明显提高材料的耐腐蚀能力,这一现象受到极大关注。同时,合金元素Cr[30]、Mo[38]、W[38]以及稀土元素Y[23]等都对非晶合金钝化起到一定的稳定作用。另外,少量元素的添加可以极大地提高非晶合金的玻璃形成能力(glass⁃forming ability,GFA)[39]。铁基非晶合金中添加少量的稀土(如Y或Er等)可使临界尺寸从2mm最大变为12mm[19]。Scully等[40]认为非晶合金具有优异的耐腐蚀性能的原因主要有两点:一是形成单相固溶体,成分、结构均匀,没有第二相等缺陷;二是对有益合金元素具有较大的固溶度。非晶合金属过饱和固溶体,对合金元素的固溶能力远超过晶态合金的极限。尽管合金元素或成分决定着非晶合金腐蚀性能的优劣,但非晶态结构本身的影响也值得关注。
另外,铁基非晶合金最大的缺点是无加工硬化能力,室温形变无明显的宏观塑性,发生剪切带引起的失稳扩展,导致灾难性断裂。已报道铁基块体非晶态合金的强度最高可达4.85GPa[41],仅仅低于Co⁃Fe⁃Ta⁃B块体非晶态合金的断裂强度,而高于其他块体非晶态合金和晶态合金。铁基块体非晶态合金的室温压缩断裂具有明显的脆性断裂特征和多个断裂面[42]。常规晶态金属材料断裂前会发生一定的塑性变形和韧性,而铁基非晶合金材料都会发生突然的断裂,这将导致灾难性的破坏。因此,提高铁基非晶合金的塑性和韧性对其作为结构材料的应用是极其重要的。