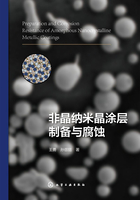
3.2 AC-HVAF非晶涂层制备
AC⁃HVAF喷涂法制备涂层,在保留HVOF喷涂法优点的同时,可获得更高致密度和更低氧化物含量的高质量涂层。鉴于AC⁃HVAF喷涂法制备的优点,能否制备性能优异的耐蚀耐磨涂层,很值得我们关注。下面主要通过AC⁃HVAF喷涂法制备非晶金属涂层,研究喷涂工艺、涂层厚度等对涂层结构特征的影响,分析涂层微观结构特征、腐蚀及硬度行为。
3.2.1 AC⁃HVAF非晶涂层制备过程
(1)涂层制备过程
用纯金属在电磁感应炉内熔炼制备Fe54.2Cr18.3Mo13.7Mn2.0W6.0B3.3C1.1Si1.4(质量分数)母合金。通过气体雾化法制备非晶粉末,用于超音速热喷涂的粉末粒度小于45μm。
AC⁃HVAF热喷涂设备采用美国Kermetico Inc.公司生产的AcuKote AK02T喷涂系统(图3⁃11)。喷枪选用AK⁃07⁃03型,喷枪配置3⋕燃料室,枪管长度200mm。采用AK⁃02T控制系统,控制系统一体化设计,空气/氮气和气体燃料采用独立空间与电气部分隔离,用PLC自动控制,并可以监测燃烧室压力。送粉器为Thermach型AT1200HP送粉器,送粉压力150psi(1psi=6.895kPa)。Zimmer丙烷汽化器型号为Z40P⁃UL⁃CE,附带3630K58钢瓶加热器。

图3⁃11 AC⁃HVAF喷涂过程
AK⁃07 AcuKote⁃HVAF喷枪能够通过压缩空气和燃气燃烧产生的高速喷束,加热非晶金属或者金属陶瓷粉末从而获得涂层。主燃料气体为丙烷,压缩空气和主气的混合物通过多孔陶瓷板进入燃烧室,经由火花塞初始点燃混合气体后,该陶瓷板被加热到混合气体的燃点以上,然后持续点燃混合物(形成激发燃烧),喷涂粉末,预先与次气(氢气)混合,被轴向注入燃烧室,在燃烧室被加热,加速进入喷嘴,通过与基体撞击,喷涂粒子最终形成涂层。
喷涂基体材料选用316L不锈钢(00Cr17Ni14Mo2)。基体的表面状况对喷涂层的结合力等性能有直接影响。热喷涂涂层与基体的结合主要以机械结合为主,熔融或半熔融的涂层材料微粒与基体碰撞和冲击变形后,与基体表面啮合而黏附,提高工件表面粗糙度及其净化程度,“抛锚”作用能力强,进而结合力提高。
为了对比实验,特制备WC涂层,粉末为德国H.C.Starck GmbH生产的WC⁃10Co⁃4Cr金属陶瓷粉末。制备时采用内衬硬质合金球磨罐,采用湿式球磨方式进行球磨制备,制备的粉末粒度为5~30μm。用于AC⁃HVAF热喷涂的具体喷涂参数见表3⁃2。
表3⁃2 AC⁃HVAF喷涂参数

非晶涂层中非晶相含量高低取决于喷涂工艺和涂层厚度。为了反映喷涂工艺和喷涂厚度对非晶涂层性能的影响,在不改变其他参数的前提下,制备了空气/燃气比分别为1.16∶1(C1)、1.17∶1(C2)和1.18∶1(C3)时的涂层,并同时制备了三种不同厚度的非晶涂层150μm(C150)、250μm(C250)和350μm(C350),通过性能分析,以此确定最佳喷涂工艺和喷涂厚度。
(2)性能测试
用德国ZEISS Axiovert 25 CA光学显微镜和日立S⁃3400Ⅱ扫描电子显微镜(SEM)观察试样组织结构和腐蚀后表面形貌。XRD分析在RINT2000衍射仪上进行,采用Cu Kα射线源(λ=0.1542nm),扫描速度为4°/min。条带样品的玻璃化转变和晶化行为是在德国Netzsch⁃404C型高温差示扫描量热分析仪(DSC)上测试完成的。利用维氏显微硬度计MVK⁃H3对条带进行硬度测试,所施压力为100g,持续时间为10s。
腐蚀性能测试在CS350电化学测试系统上进行。条带样品在进行动电位极化行为测试前均需经过1000⋕以上的砂纸精细打磨,随后用石蜡混合松香封样,经过酒精和丙酮清洗、蒸馏水清洗等一系列准备过程。动电位极化曲线(PD)扫描速率为0.167mV/s,扫描电位范围为相对于开路电位-0.25~+1.2V。
3.2.2 制备工艺对非晶涂层结构特征的影响
(1)非晶涂层结构特征
图3⁃12是气体雾化法制备的铁基非晶合金粉末的SEM照片和XRD图谱,可以看出所选用的粉末粒度小于30μm。大部分粉末为球形或近球形颗粒且表面光滑,只有个别较大颗粒上面附着一些小颗粒,即卫星组织。这主要是因为在喷涂过程中,不同尺寸的颗粒在气体紊流作用下相互碰撞,小的颗粒具有相对较高的凝固速率,很容易贴附在熔融状的大颗粒表面,形成黏结在一起的状态。这些特征说明非晶粉末会具备良好的流动性,将十分有利于热喷涂。
从XRD曲线上可以看出,在2θ=45°附近非晶粉末和涂层均存在一个较宽的且漫散的衍射峰,说明形成非晶结构。其中非晶粉末的XRD图谱中无明显的布拉格衍射峰的出现,表明所有粉末在X射线分辨率下基本为非晶态结构。这主要是由于气体雾化法具有较高的冷却速率(约105K/s),因此金属液滴在快速凝固中较易形成非晶态。而在涂层的XRD图谱中出现了一些尖锐的晶体峰,说明其中存在一定的晶体相。晶体相主要由Fe2C、Cr7C3、 M23C6、Cr2B和极少量的氧化物组成。涂层中氧化物的存在不利于非晶结构的形成。涂层的晶化是由于在喷涂过程中,随喷涂过程的进行,后序的热量对已沉积涂层的局部热处理所致,厚度越厚,这种晶化现象越严重。在制备非晶涂层过程中,要求涂层具有较高的玻璃形成能力,这样才能保护制备的高非晶结构的涂层。但在实际中,由于喷涂过程后序的热能不能有效散射出去,导致最终形成的涂层以层状的形式存在。

图3⁃12 非晶粉末的SEM照片和XRD图谱
由于非晶合金的原子结构处于亚稳态,在升高温度时会发生晶化,向稳定状态转变。一般将合金晶化开始温度与玻璃化转变温度之间的差值定义为过冷液相区(ΔTx=Tx-Tg),用来衡量非晶合金的热稳定性。过冷液相区越大,非晶合金的热稳定性越大。但非晶合金晶化后,其很多优异性能会发生不利转变,如电阻升高、耐腐蚀性能下降等。非晶合金条带在加热情况下发生晶化现象,这种晶化是通过合金内原子扩散进行的。
图3⁃13是非晶涂层以及对应条带的DSC曲线。在DSC曲线上,所有样品均在600℃与800℃温度区间内表现出2个明显的晶化峰。涂层晶化峰的面积则有所减小,说明在涂层形成过程中确实发生了一定的晶化转变。通过以下公式可以定量地计算出涂层中非晶相含量,Vf=ΔHcoating/ΔHribbon,其中ΔHcoating为涂层中的晶化峰面积,ΔHribbon为条带的晶化峰面积。经计算,涂层的非晶相含量为78.9%。

图3⁃13 条带和涂层的DSC曲线
(2)制备工艺对非晶涂层性能的影响
AC⁃HVAF喷涂技术比较适合制备铁基非晶纳米晶涂层,主要是由于在热喷涂过程中,单个粉末颗粒在熔化冷却时速率接近107K/s,远高于其临界冷却速率,满足非晶合金的形成条件。制备具有特定性能的非晶涂层需要对AC⁃HVAF喷涂过程、工艺参数与涂层结构性能之间的关系有一定的了解。涂层的结构又主要取决于喷涂过程中颗粒撞击基体瞬间的物理和化学状态,比如喷射速率、颗粒温度、熔化以及氧化程度等。这些参数的变化与喷涂参数相关,如空气/燃气流量比、喷涂距离、送粉速率和粉末颗粒粒径等。所以,要想获得高质量的非晶涂层,研究这些喷涂工艺参数对涂层结构与性能的影响是至关重要的。本节主要考虑空气/燃气流量比对非晶涂层性能的影响。
① 涂层微观结构
空气/燃气比在AC⁃HVAF喷涂过程中具有非常重要的影响,主要与涂层的熔化状态、氧化程度和孔隙率相关。不同空气/燃气比(1.16、1.17和1.18)所制备涂层的表面SEM图及表面金相特征见图3⁃14。
由图3⁃14可知,空气/燃气比极大地影响了非晶涂层的微观组织结构。未熔颗粒随空气/燃气比的增加而呈增加趋势,见图3⁃14(a)、(c)、(e),这主要与燃气和喷涂颗粒之间的热传递过程相关。空气/燃气比低时,燃气过量容易导致涂层过热而氧化;而空气/燃气比高时则有可能热量不足而导致过多未熔颗粒出现。实际上,空气/燃气比是影响涂层质量的关键因素。对于传统HVOF喷涂法,制备涂层组织结构中往往会形成明显的氧化物带或层,但对于本文的AC⁃HVAF制备法来说,制备的涂层氧化程度明显降低。图3⁃14(b)、(d)、(f)为涂层抛光后表面的金相图,图中黑色点状区域为孔隙,一般涂层中的氧化物为灰色带状,从图中可以看出,所制备的涂层氧化物含量极少。孔隙率大小与制备工艺有一定关系,空气/燃气比过低或过高时,所制备涂层孔隙率均较高,在空气/燃气比为1.17(C2)时涂层孔隙率最小(0.95%)。适当的空气/燃气比是制备低孔隙率且高质量非晶涂层的关键。
不同空气/燃气比所制备涂层的侧面SEM图见图3⁃15。由图可知,三种工艺所制备的涂层,基体与涂层界面结合良好,无明显的宏观孔洞和裂纹形成。热喷涂涂层主要由变形良好的粒子相互搭接、堆积进而形成典型的层状结构,层与层也无明显的氧化物夹杂带出现。
② 涂层XRD及DSC图谱
不同喷涂参数制备涂层的XRD图谱见图3⁃16(a)。可知,条带和非晶涂层的XRD图谱均在45°附近呈现出一个漫散射峰,说明制备的非晶涂层和条带具备相似的非晶结构。非晶涂层的XRD图谱伴随有个别尖锐峰,说明涂层含有少量纳米晶体相。这些纳米晶体相形成,是由于涂层在制备时,后序喷涂过程中的热量对基体局部加热的作用。由图3⁃16(a)可知,不同制备工艺制备的非晶涂层,喷涂参数如空气/燃气比不同,这些纳米晶体相的数量和含量有所不同。在空气/燃气比比较低时(C1),晶体峰更为尖锐,说明较低的空气/燃气比不利于非晶相的形成。空气/燃气比低,燃气含量高,过高的热量会使得较多的未熔颗粒在高温下发生晶化,致使涂层晶化相形成的概率也增加。

图3⁃14 不同工艺制备涂层的表面特征
由图3⁃16(b)可知,三种涂层表现出较为类似的热行为,均呈现出明显的固⁃固相变的放热峰,说明涂层中确实存在一定量的晶体相。通过比较三种涂层晶化峰的热流积分面积,可估算出所制备的涂层中非晶相含量的多少。通过计算,涂层C1、C2和C3非晶相含量分别为65.2%、79.6%和75.3%。可见,与上面涂层微观结构分析和XRD图谱测试结果一致,喷涂工艺与涂层非晶相含量有一定关联。涂层C2具有最高的非晶相含量,说明C2的涂层制备工艺可以实现最大程度的非晶结构形成。
③ 制备工艺对涂层腐蚀行为的影响
图3⁃17示出了不同材料在3% NaCl溶液中的动电位极化曲线。由图可知,所有材料均呈现出明显的钝化行为。304和316L不锈钢点蚀电位较低,约0.2V和0.4V,说明其抵抗

图3⁃15 不同工艺制备涂层的侧面SEM特征

图3⁃16 不同参数制备涂层的XRD图谱和DSC曲线
局部腐蚀的阻力降低。非晶涂层点蚀电位较高(约1.1V),说明涂层在3% NaCl溶液中具有较高的局部腐蚀抗力,非晶涂层在NaCl溶液中抵抗局部腐蚀的阻力远高于304和316L不锈钢。

图3⁃17 不同参数制备涂层及不锈钢的动电位极化曲线
不同工艺制备的非晶涂层点蚀电位相差不大,反映出涂层抵抗局部腐蚀能力相当。但涂层钝化电流密度对空气/燃气比敏感。由图可知,涂层的钝化电流密度沿C2、C3和C1的顺序依次增加,由10-5A/cm2增大到10-3A/cm2,所有涂层的钝化电流密度均远高于不锈钢(约10-6A/cm2),说明涂层的均匀腐蚀抗力明显降低,主要归因于涂层中缺陷(如孔隙)的影响。可以看出,涂层C2具有最低的钝化电流密度,耐蚀性最优。
3.2.3 厚度对非晶涂层性能的影响
在非晶涂层制备过程中,涂层晶化在所难免,这主要是由于随着喷涂过程的进行,后序的热量对已沉积涂层形成局部热处理。喷涂过程后序的热量不能有效散射出去,这种局部加热是涂层制备过程中不可避免的,尤其在涂层厚度增加的情况下,所以制备非晶涂层时,适当的厚度控制是保证涂层优异耐蚀性能的前提。
为了反映厚度对非晶相形成的影响,特制备了150μm、250μm和350μm等三种不同厚度的非晶涂层。图3⁃18(a)是不同厚度涂层的XRD图谱。可知,非晶粉末和三种涂层在45°均呈现出明显的漫散射峰,说明其主要为非晶结构。与非晶粉末相比,涂层XRD图谱出现少量晶化峰。在所测试的三种厚度涂层中,随厚度增加,晶化峰数量和强度稍有增加,C350涂层晶化程度较高。三种涂层DSC曲线见图3⁃18(b)。三种厚度的非晶涂层经过加热,DSC曲线出现明显的固⁃固相变放热峰,发生了明显的晶化转变。C150涂层放热峰面积最大,说明其非晶相含量最高,C250涂层次之,C350涂层最小。
三种涂层侧面SEM背散射照片见图3⁃19。可以看出,不同厚度非晶涂层与基体界面结合良好,涂层致密,没有出现明显的界面结合缺陷。非晶涂层厚度的增加并没有对界面结合缺陷产生明显的影响。
图3⁃20显示的是三种厚度非晶涂层在3% NaCl溶液中的动电位极化曲线。三种非晶涂层均呈现出稳定的钝化特征,具有相同的点蚀电位,约1.1V。钝化电流密度对涂层厚度变化敏感,薄的C150非晶涂层钝化电流密度最小,C250涂层次之,C350涂层最大。这反映出非晶相含量对涂层钝化电流密度有至关重要的影响,薄的涂层具有最高的非晶相含量则呈

图3⁃18 不同厚度涂层的XRD图谱和DSC曲线

图3⁃19 不同厚度涂层的侧面SEM特征
现出较低的钝化电流密度。
涂层非晶相含量之所以受到厚度的制约,主要因为在喷涂过程中粒子加热和冷却过程时间短,粒子结晶和凝固均为非平衡过程。在较高冷速下,涂层中才会形成非晶结构。当第一层薄片沉积形成后,扁平粒子的冷却和传热主要是通过基体表面来完成的。此时的热量传输较快且冷却速率达到最大(通常在106K/s以上),基体温度升高不太明显,可以获得接近完全的非晶结构。随着喷涂道次的增加,已沉积涂层和基体之间的热导率变低,导致涂层内部沿厚度方向形成一个温度梯度且冷却速度会降低。在后续颗粒的沉积作用下,绝热再辉和晶化现象不可避免,再加上非晶合金低的热导率,最终导致涂层非晶相含量会随厚度增加而降低,可以说利用热喷涂方法难以获得较厚的且具有完全非晶结构的合金涂层。

图3⁃20 不同厚度涂层的动电位极化曲线
3.2.4 AC⁃HVAF WC涂层结构和性能研究
(1)WC涂层结构特征
图3⁃21(a)为WC⁃10Co⁃4Cr粉末的SEM照片,可以看出,粉末为圆形或近圆形,球形度较高。多数颗粒为松散分布,无黏附或团聚现象。所有粉末粒径均在15μm左右,大小均一。

图3⁃21 WC⁃10Co⁃4Cr粉末SEM和XRD
一般粉末粒度分布均匀,可以有效提高送粉和喷涂的效率,粉末熔化扁平铺展效果好,更易获得低氧化、高结构致密的涂层。从粉末表面观察,粉末表面粗糙多孔,这种多孔的结构有利于粉末在喷涂火焰的焰流中的吸收和传递热量,减少涂层中一些未熔颗粒的数量,进而提高喷涂涂层的质量。为了分析涂层厚度的影响规律,采用AC⁃HVAF法制备了50μm和100μm两种厚度涂层,所制备WC⁃10Co⁃4Cr涂层的表面及侧面SEM如图3⁃22(a)、(b)所示。

图3⁃22 WC⁃10Co⁃4Cr涂层表面及侧面SEM照片
从图3⁃22(a)、(b)涂层喷涂态的表面形貌看,两种厚度涂层表面喷涂形貌并无明显差别。从涂层表面喷涂态形貌分析,可以看出颗粒在撞击喷涂基体后,绝大部分已充分摊平,呈小薄饼状,说明颗粒在喷涂焰流中进行了充分熔融并且发生变形,这种喷涂特征使得颗粒具有良好的填充孔隙的能力,颗粒之间相互咬合作用也比较强,从而使得涂层结构致密。从涂层截面的背散射SEM照片看[图3⁃22(c)、(d)],涂层无明显的层状分布特征,涂层致密,沿着每个层间的边界分布着一些小块的黑色区域,这些区域可能是小的孔隙,孔隙小且分布均匀。另外,从侧面图像分析可知,两种厚度涂层孔隙率相差不大。涂层与界面结合良好,这些特征源于良好的球形粉末结构和适当的HVAF喷涂工艺参数。
WC⁃10Co⁃4Cr粉末及制备涂层的XRD图谱见图3⁃21(b)。经过对XRD图谱分析,可以看出,粉末和制备涂层物相的峰位基本相同,主要物相为WC,还含有少量的Cr7C3碳化物相、CrCo固溶体和Co6W6C脆性相等,二者的物相基本一致,经过AC⁃HVAF喷涂,没有使粉末成分发生明显变化。在2θ=44°处涂层的XRD图谱出现一个峰强度低、较宽泛的漫散射衍射峰,这可能是由于在喷涂过程中,熔融的固体颗粒撞击基体,颗粒以极高的速度冷却从而形成少量的非晶或纳米晶相所致。
对于传统的HVOF法喷涂,制备过程WC相极易出现脱碳现象。通过适当调整工艺参数均得到只出现少量W2C脱碳相的涂层[16]。而本文采用的AC⁃HVAF法制备的涂层则不存在W2C脱碳相,这表明AC⁃HVAF喷枪与HVOF喷枪相比,更易于获得相结构较为单一和高性能的涂层。这源于AC⁃HVAF法具有较低的焰流温度和较高的颗粒速度,粉末在焰流飞行过程中氧化程度小。
(2)WC涂层耐蚀性能
两种厚度WC⁃10Co⁃4Cr涂层在3% NaCl溶液中的动电位极化曲线见图3⁃23。

图3⁃23 不同厚度WC⁃10Co⁃4Cr涂层的动电位极化曲线
两种涂层均呈现出明显的钝化特征,但钝化行为并不稳定,点蚀电位较低,约0.9V。涂层的钝化电流密度对涂层厚度变化敏感,厚的C100涂层钝化电流密度小于C50。这与上面所制备的非晶涂层结果不同。对于非晶金属涂层,薄的涂层非晶相含量高,因而钝化电流密度低。而对于WC⁃10Co⁃4Cr涂层,厚涂层低的钝化电流密度,主要是由于涂层厚度对Cl-扩散阻挡作用所致。一般来说,在涂层孔隙变化不大的情况下,厚涂层对于O2和Cl-传输的障碍作用要强于薄涂层,因此呈现出低的钝化电流密度,耐蚀性提高。
非晶金属和金属陶瓷涂层的硬度测试结果见图3⁃24。
由图可知,基体材料维氏硬度为360HV左右;非晶金属涂层平均硬度为1400HV,最高可接近1600HV;金属陶瓷涂层平均硬度则达2000HV。虽然非晶金属涂层硬度比基体高3倍多,但金属陶瓷硬度远高于非晶金属涂层。非晶金属和金属陶瓷硬度均非常高,除了喷涂材料成分之外,主要与喷涂所采用的方法和喷涂工艺参数有关。AC⁃HVAF法制备的涂层致密、孔隙率小,更易呈现出较高的硬度,远高于HVOF法制备的涂层(显微硬度HV0.3 1322)[16],以及气体燃料DJ喷枪制备的WC⁃10Co4Cr(显微硬度为HV0.3 1265[17])。

图3⁃24 非晶金属涂层(HVAF⁃AM)和金属陶瓷(HVAF⁃WC)涂层硬度比较