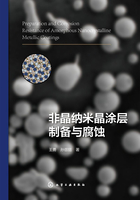
2.2 成分影响非晶合金腐蚀性能
普遍认为,Mo的添加有效地提高了钝化膜的稳定性和均匀性,因此提高了腐蚀抗力。但Mo对钝化膜性能影响的研究多集中于传统不锈钢领域,添加Mo能有效提高钢点蚀抗力一个必不可少的条件是钢中存在足够量的Cr[65]。还有观点认为,Mo添加后在钝化膜外侧形成一种阳离子选择性的Mo,抑制了阴离子(Cl-、OH-)的吸附,进而有利于内层Cr氧化物膜层的形成。这种双极性的膜层有效地稳定了氧化物相,使得钝化膜抵抗点蚀作用更强。然而,在Fe⁃C非晶合金中,在没有Cr存在条件下,添加一定量的Mo也发生了阳极钝化,极大地提高了腐蚀抗力[66]。对于Mo在钝化膜中的本质还没有一致认同的观点,一些学者认为形成难溶的富集Mo物质[如Mo
、Mo
、MoO(OH
,Mo2
和FeMo
]是添加Mo能维持钝态的主要原因。况且,富Mo的钝化膜随时间变化可以转变为富Cr的氧化物膜层[72]。然而,其他学者通过实验得出,在一些不锈钢[73]和非晶合金的钝化膜层中并没有富Mo的物质出现。另有少数学者推断,Mo具有较高的金属键,可以在缺陷的局部区域优先形成,从而抑制阳极的溶解过程[74]。这些都说明对于Mo在钝化膜中的作用目前还没有得到广泛的认识。况且,非晶合金中Mo对腐蚀机理的作用可能与普通的晶体不同。过量的Mo添加会引起非晶合金阳极电流密度的增加,降低腐蚀抗力。非晶合金中Mo的添加减小了钝化膜层的厚度[75],对于铁素体不锈钢则对膜层厚度无影响[76],但对于奥氏体不锈钢则呈现出增加膜层厚度的趋势[65]。所以说,在非晶合金中,Mo的作用究竟如何还有待于进一步的实验研究。
在普通的不锈钢中,Mn是一种奥氏体稳定化元素,添加过量后由于形成MnS夹杂物,致使不锈钢腐蚀抗力降低[77]。对于非晶合金来说,添加Mn后并没有形成诸如MnS夹杂的情况,所以Mn对于非晶合金腐蚀影响规律的研究也是很值得期待的。与Mo一样,W的添加也可以极大地提高非晶Fe⁃P⁃C合金的腐蚀抗力[78]。钝化膜外层的W氧化物由于溶解速率低,可抑制钝化膜层的进一步溶解[79]。对于非晶合金[78]和不锈钢[80,81],W可以提高其在含氯介质中的点蚀抗力,对于钝化电流密度和点蚀电位影响则不大。与Mo相似,W的添加也可以增加膜层内的Cr氧化物的含量[82]。除此之外,添加Mo和W后,还可以更有效地提高合金的硬度,从而提高耐磨性。这更可扩大铁基非晶合金在耐磨领域的应用。但在同时考虑硬度和耐蚀性的前提下,Mo、Mn和W的添加对于耐蚀性能和硬度的影响规律以及相应的作用机理,目前还没有相关的系统研究报道。
本部分主要研究添加Mo、Mn和W对于铁基非晶合金耐蚀性和硬度的影响规律,优化耐蚀耐磨合金成分,以期为扩大铁基非晶合金在耐蚀/耐磨领域的应用提供参考。
2.2.1 非晶条带制备
(1)不同成分条带制备
以Fe49.6Cr18.1Mo7.4Mn1.9W1.6B15.2C3.8Si2.4(原子分数,%)合金成分为基础,研究Mo、Mn、W含量变化对其腐蚀性能和硬度的影响规律。Mo、Mn、W含量变化遵照以下配比(原子分数):
① Fe49.6-xCr18.1Mo7.4+xMn1.9W1.6B15.2C3.8Si2.4(x=-2,0,2,4,6;分别记为:Mo5.4,Mo7.4,Mo9.4,Mo11.4,Mo13.4)。
② Fe49.6-xCr18.1Mo7.4Mn1.9+xW1.6B15.2C3.8Si2.4(x=-1.9,0,0.95,1.9 ;分别记为:Mn0,Mn1.9,Mn2.85,Mn3.8)。
③Fe49.6-xCr18.1Mo7.4Mn1.9W1.6+xB15.2C3.8Si2.4(x=-1.6,0,1.6,3.2;分别记为:W0,W1.6,W3.2,W4.8)。
按上述配比,用纯金属元素在真空电弧炉中熔炼制备母合金铸锭,然后在真空单辊急冷装置进行非晶条带制备。
(2)性能测试
条带样品的XRD在Rigaku D/max2400衍射仪上进行,用Netzsch⁃404C型高温差示扫描热量分析仪测试条带的DSC曲线。腐蚀性能测试在PAR Model 2273工作站上进行,实验介质选择3% NaCl溶液,包括动电位极化曲线和电化学阻抗谱。用ESCALAB250光电子能谱分别测试条带在3% NaCl溶液中0.6V(SCE)电位下阳极极化104s后的钝化膜特性。
利用维氏显微硬度计MVK⁃H3对条带进行硬度测试,所施压力为100g,持续时间为10s。每个样品测试不同区域的10个数值,最后取平均值。测试前,样品采用金刚石抛光至无划痕,呈镜面状态。
2.2.2 条带的非晶结构表征
图2⁃19是不同Mo、Mn和W含量所制备非晶条带的XRD图谱。可以看出,基本上所有条带XRD图谱(除了Mo13.4、Mn0和W4.8)上均无尖锐衍射峰,在2θ=40°~50°的范围内显示出漫散的衍射峰,表明其均为完全非晶态结构。

图2⁃19 不同Mo、Mn和W含量制备的非晶合金条带的XRD图谱
不同Mo、Mn和W含量所制备非晶条带的DSC曲线见图2⁃20。由图可见,几乎所有条带的DSC曲线都具有明显的放热峰特征,通过比较放热峰的面积,可以比较出不同条带的非晶相含量的相对多少。由比较结果可知,Mo13.4、Mn0和W4.8制备的条带放热峰面积较其他的小,所以非晶相含量相对较低,其他不同元素含量所制备的条带在加热情况下基本发生完全晶化现象,可以认为是完全非晶的特征。非晶相的形成对Mo元素的含量变化不敏感,但过量的Mo则明显降低了放热峰的面积[图2⁃20(a)]以及增加了晶化相出现的概率[图2⁃19(a)],说明过高的Mo降低了非晶条带的玻璃形成能力。随Mn含量的增加,晶化相越来越少[图2⁃19(b)],放热峰面积则越来越大[图2⁃20(b)],说明增加Mn元素含量可以提高条带的玻璃形成能力。随W含量的增加,晶化相数量增加[图2⁃19(c)]且放热峰面积减小[图2⁃20(c)],说明增加W元素含量也相应降低了条带的GFA。

图2⁃20 不同Mo、Mn和W含量制备的非晶合金的DSC曲线
2.2.3 硬度的影响
不同Mo、Mn和W含量制备非晶条带的硬度如图2⁃21所示。由图可知,随Mo含量的增加,条带的硬度呈增加趋势。当Mo含量低于9.4%(原子分数)时,增加幅度较大;但当其含量超过9.4%(原子分数)以后,硬度增加趋于缓慢,进一步增加Mo含量对硬度提高程度不大。Mn含量的添加对硬度影响不大,说明Mn含量的增加与硬度之间没有必然的联系。W的添加可以极大地提高条带的硬度,硬度随W含量的增加而急剧增加,高的W含量可以使条带获得更高的硬度。

图2⁃21 不同Mo、Mn和W含量制备的非晶合金的硬度
2.2.4 电化学腐蚀行为
不同Mo、Mn和W含量所制备非晶条带在3% NaCl溶液中的动电位极化曲线如图2⁃22所示。可以得出,条带的钝化电流密度对各元素含量的变化敏感。对于Mo来说,条带的钝化电流密度随Mo含量的增加呈现出先减小后增加的趋势。Mo9.4合金钝化电流密度最小(约4×10-8A/cm2)。随Mo含量的进一步增加,钝化电流密度反而增加,Mo13.4合金的

图2⁃22 非晶合金条带在3% NaCl溶液中的动电位极化曲线和电化学阻抗谱
钝化电流密度达到最大(约3×10-5A/cm2),见图2⁃22(a)。Mn含量不同时,条带的钝化电流密度随Mn含量的增加而降低,Mn3.8合金的钝化电流密度最小(约5×10-8A/cm2),见图2⁃22(b)。
与不同Mo含量的规律类似,条带的钝化电流密度随W含量的增加也呈现出先减小后增加的趋势,W3.2合金具有最小的钝化电流密度(约5×10-8A/cm2),进一步增加W含量会导致钝化电流密度急剧增加,W4.8合金的钝化电流密度达到最大(约2×10-5A/cm2),见图2⁃22(c)。图2⁃22中所有电化学阻抗谱的测试结果与极化曲线相一致。
2.2.5 钝化膜表征
钝化膜以及金属基体中各金属元素和氧的浓度分布如图2⁃23所示。与基体相比,钝化膜中的Fe、Cr和Mo的含量急剧下降。根据O含量下降到最表面层一半处作为钝化膜厚度,所有条带形成的钝化膜厚度都约为2nm,说明合金元素的添加对膜层的厚度影响不大。恒电位腐蚀后的膜层经氩离子溅射20s后不同元素含量时典型的Fe 2p、Cr 2p和Mo 3d精细谱峰如图2⁃24所示。金属态Mo和W的谱峰强度相对其氧化态较高,说明钝化膜内层或界面上有部分未完全氧化的Mo和W存在,氧化态的Mn谱峰强度则高于金属态的Mn。

图2⁃23 非晶合金条带在3% NaCl溶液中表面层各组元的深度分布

图2⁃24 元素含量对表面层中Mo、Mn和W状态的影响
另外,Mn 2p和W 4f精细谱峰的强度均随Mn、W含量的增加而增加,说明合金中添加相应的Mn和W后,对应膜层中的含量也增加。对于Mo来说则不同,Mo9.4合金的钝化膜中Mo含量最高,随后继续添加的Mo则无利于其在钝化膜中的形成。
2.2.6 合金元素与耐蚀性及硬度的关系
不同Mo、Mn和W元素制备条带的钝化电流密度与其含量关系见图2⁃25。
由图可知,非晶合金条带钝化电流密度随元素含量发生一定规律的变化。随Mo、W含量的增加呈先减小后增加的趋势,在Mo、W含量(原子分数)分别为9.4%和3.2%时,钝化电流密度最小。与之不同的是,钝化电流密度随Mn含量的增加则呈一直降低趋势。这说明各个元素含量的变化影响了非晶合金的腐蚀行为,可以通过调节合金元素的含量来实现优化合金耐蚀性的目的,比如选择Mo9.4、Mn3.8或W3.2合金,则可实现制备最佳的耐蚀性能的非晶合金。
Mo是不锈钢中经常添加的一种非常重要的合金元素,可以有效抑制Cl-点蚀,一直以来受到学者的广泛研究。在钝化过程中,Mo可以抑制Cr的溶解,进而提高腐蚀抗力和钝化能力。Mo所形成的难溶氧化物覆盖了点蚀部位,抑制了点蚀的发展,发生再钝化。但非晶合金中过量的Mo提高了阳极电流密度,进而降低腐蚀抗力。本文的结果与此类似,超过9.4%(原子分数)的Mo降低了非晶合金条带的腐蚀性能,这主要与Mo在钝化膜中存在的本质相关。

图2⁃25 元素含量与钝化电流密度的关系
添加W也可以提高非晶合金[77]和不锈钢[81]在含Cl-介质中的点蚀抗力。对于含或不含Cr的Fe⁃P⁃C非晶合金,添加W后均提高了其腐蚀抗力[78]。Fe⁃8Cr⁃7W⁃13P⁃7C非晶合金的钝化电流密度随W含量的增加而降低[82],主要由于W抑制了合金的溶解过程。随W含量的增加,Cr在钝化膜中富集,含W合金的钝化是通过将空气中形成的膜转变为优先溶解Fe后的富Cr膜层。本文不同的是,高含量的W(4.8%)降低了非晶合金的腐蚀抗力,这主要是由于高含量的W降低了条带的玻璃形成能力(GFA),见图2⁃19(c)、图2⁃20(c),低的GFA导致条带的腐蚀性能下降。原子的局部构型极大地影响GFA[83],由于Mo和W的原子半径与Fe相差不大,少量的添加量可以替换无序结构中的Fe,但过量地添加则会产生明显的局部结构紊乱甚至破坏,影响GFA。所以说,适量的Mo和W有益于GFA的提高,但过量的添加则是有害的。
Mn是不锈钢常用的一种强奥氏体稳定化元素,但添加Mn极大地降低了不锈钢的耐蚀性,主要是由于MnS夹杂物的形成。MnS夹杂物电化学稳定性低,易于溶解,且在夹杂物和基体界面易遭受腐蚀介质的侵蚀成为点蚀形核和发展部位[71]。另外,Fe⁃18Cr⁃xMn(x=0,6,12)合金的点蚀抗力随Mn含量的增加而降低,主要是由于Mn氧化物的出现成为点蚀的形核部位[84]。而Mn的添加恶化了Fe⁃Mn合金的腐蚀抗力也主要是由于钝化膜中Mn氧化物的存在[85]。这些结果说明Mn多以有害元素的作用存在于Fe⁃Cr和Fe⁃Mn合金中,主要原因是这些硫化物和氧化物的形成。但在非晶合金中,增加Mn的含量极大地提高了FeCrMoMnCBY在1mol/L HCl溶液中的腐蚀抗力[86]。本文中Mn的添加对于腐蚀抗力的提高也是非常有益的,这主要是由于在非晶合金中Mn硫化物和氧化物夹杂的不利影响被消除,当然也与Mn在钝化膜中存在的本质有关。
(1)合金元素与钝化膜稳定性
非晶合金的耐蚀性主要取决于钝化膜的稳定性,钝化膜的稳定性则是基于材料在腐蚀介质中的自发钝化的能力,所形成的膜或者自身稳定或者可以转化为稳定的膜层。Cr是材料中具有高钝化能力最有效的合金元素,对于不含Mo、Mn和W合金元素的合金,由于Fe和Cr的溶解速率不同,最终形成Cr富集的钝化膜层,提高腐蚀抗力[87]。当材料中加入合金元素后,合金的溶解过程受到抑制且富Cr钝化膜层更为稳定,点蚀抗力得到提高。Mo的添加也改善了钝化膜层的结构,使其更耐Cl-的侵蚀。Mo还优先富集于一些易于溶解的缺陷部位,加上其高的金属键,最终降低了合金的阳极溶解速度[74]。另外,富Mo的钝化膜层随浸泡腐蚀时间的增加,还可以转化为更为稳定的富Cr钝化膜层[72]。
影响钝化膜稳定性的另一个重要特征是膜层具有稳定的内层或外层结构,起到一个有效地阻挡介质扩散或浸透的作用。由图2⁃23可知,所有条带表面的钝化膜厚度都约为2nm,说明合金元素添加并没有影响其表面形成钝化膜的厚度。根据图2⁃24各元素精细谱峰中每个谱峰所围成的面积,可以计算出各个元素不同价态在钝化膜层中所占的比例,计算结果见图2⁃26。

图2⁃26 钝化膜层中主要组元状态及含量分布
由图2⁃26可知,条带的钝化电流密度与钝化膜成分之间存在必然联系,即合金耐蚀性与其表面形成的钝化膜成分密切相关,确切地说,是与钝化膜层中形成的特定价态的氧化物含量有关。图2⁃26(a)反映的是不同Mo含量所形成钝化膜层中氧化物价态的含量分布。结合图2⁃25可以得出,合金耐蚀性与Mo含量所呈现出的规律性变化,与钝化膜层中Mo4+氧化物含量一致,并与Mo6+氧化物含量趋势相反。这说明膜层中Mo4+氧化物是稳定钝化膜的主要因素,保证了合金耐蚀性的提高。Mo9.4合金具有最高耐蚀性的原因也是由于膜层中形成了较多的Mo4+氧化物。对于富集Mo膜层来说,膜层外侧形成的高价态的Mo6+(Mo)物质往往发生优先溶解[38],这种高价态Mo6+物质的过量溶解也极大地增加了合金的钝化电流密度并降低了腐蚀抗力。相反,低价态的Mo4+物质则维持了Fe⁃Cr非晶合金的钝化性能,这种具有保护性富集的Mo4+膜层[Mo
,MoO(OH
]可以有效地阻止腐蚀介质的侵蚀,从而提高腐蚀抗力。这也与第1章的结果一致,膜层中高价态的氧化物发生优先溶解,而低价态的氧化物维持钝化膜的稳定性,提高非晶合金的耐蚀性。
与Mo不同的是,膜层中Mn和W的影响则表现出不同的规律。耐蚀性与高价态Mn4+氧化物含量趋势一致,随Mn4+氧化物含量增加,耐蚀性逐渐提高,说明Mn4+氧化物的存在是保证合金具有稳定耐蚀性的主要原因。W元素的影响也呈现出类似的规律,耐蚀性与高价态W6+氧化物含量吻合,随W6+氧化物含量增加而增加。W氧化物由于具有较低的溶解速率,在膜层外层可以起到抑制膜层溶解的作用[79]。W和Mo一样,在膜层中也富集于一些活性区域,阻止了点蚀等过程的形成。另外,添加W元素后可以增加膜层中Cr氧化物的含量[82],这些都是添加W元素对于腐蚀抗力的有利影响。然而,W6+(WO3)氧化物的形成增加了WC⁃Co硬质合金的腐蚀过程[88],这说明过量的W6+氧化物不利于腐蚀抗力的提高,这也符合本文的结果,过量的W(4.8%,原子分数)元素恶化了腐蚀性能。但要注意的是,在W含量较高时,极化曲线反映出耐蚀性急剧下降,但此时W6+氧化物含量依然保持在较高的水平。结合图2⁃19的XRD可以看出,在W含量较高时,其非晶相含量明显降低,说明非晶的GFA下降,较低的非晶含量(图2⁃20)再加上高的W6+氧化物含量,最终降低了非晶合金的耐蚀性。
(2)合金元素与硬度关系
要保证铁基非晶合金应用于耐蚀耐磨环境,除了要考虑耐蚀性之外,耐磨性也是必须要关注的因素。一般用硬度来衡量材料耐磨性的高低,高的硬度可以侧面反映出材料具有高的耐磨性。所以这里除了考虑各合金元素对腐蚀性能的影响,更要分析对其硬度的作用。由图2⁃21可知,除了Mn元素之外,合金硬度与Mo、W合金元素存在一定关系。硬度随W含量增加呈急剧增加趋势,硬度随Mo含量增加也呈现出增加趋势,但过高的Mo含量(超过9.4%,原子分数)对硬度的影响幅度不大。早期的研究也表明,添加Mo和W对于提高材料硬度和耐磨性非常有益。Mo的添加可以极大地提高Co⁃Cr⁃W⁃C合金的耐磨性,增加Mo的含量可以形成类似M23C6和M6C的碳化物,替代了M7C3形式的富Cr碳化物,进而提高合金的硬度。另外,Stellite涂层具有优异的冲蚀抗力也是由于其中高硬W氧化物的存在,这些高硬物质改变了合金的微观结构,提高了合金的硬度乃至耐磨性。所以说,要想提高该非晶合金的硬度,添加适当的Mo含量以及较高的W含量是可以考虑的。
因此,要想使合金具有优异的耐蚀性和耐磨性,可以对其合金元素含量进行优化。对于Mo来说,Mo含量的增加提高了合金的硬度,但超过9.4%(原子分数)时硬度增加程度缓慢;耐蚀性方面,Mo9.4合金耐蚀性最优,之后耐蚀性急剧下降。综合起来,选择Mo9.4合金,即可以实现耐蚀耐磨性于一体的合金设计。对于Mn来说,由于Mn含量增加对硬度并没有产生影响,所以只考虑耐蚀性较优的条件,耐蚀性随Mn含量增加而增加,所以选择Mn含量为3.8%(原子分数)时即可。对于W来说,硬度随W含量增加而增加,耐蚀性也随W含量呈现出先增加后降低趋势,所以选择较高的W3.2合金,可以同时保证耐蚀性和耐磨性。综合来说,9.4% Mo、3.8% Mn和3.2% W(原子分数)是设计耐蚀与耐磨于一体合金可以参考的优选条件。但要注意的是,此实验只是单个合金因素的影响,两个或三个合金元素的综合影响还有待于进一步研究。